MANUFACTURING PROCESS
Sashi Engineering headquarters is a 15,000 square foot facility
located in Bangalore, India, and specializes in manufacturing
polyurethane & TPU products for a variety of industries. Our facility
operates several production lines that can accommodate small and
large polyurethane parts to meet your custom needs. Our machine
shop has collaborated with the advanced CNC machinery house and
software to build precision tooling and metal inserts for your molded
parts.

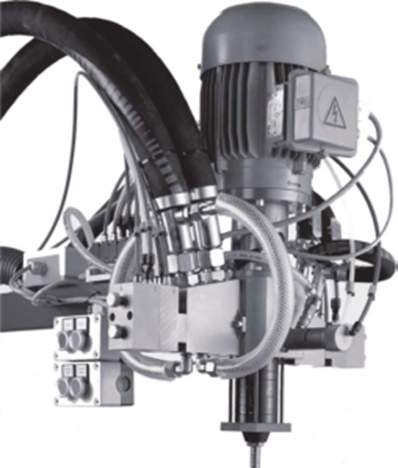
VERSATILITY OF URETHANE CASTING
A polyurethane cast can be used to maximize performance and minimize upfront costs. The casting methods
and urethanes used by Sashi Engineering allow tailoring components for the best overall performance in
various products. Polyurethanes (PUs) are in a polymer class of their own. Polyether or polyester polyurethanes
can be made depending on the choice of co-monomers used to produce them. They combine the desired
benefits of rigid materials with the elasticity, bridging the gap between polyurethane and plastics in the many
industry sectors served by these versatile polymers.
Polyurethane used in our casting processes can easily be coloured, unlike regular millable rubbers and still
exhibit better abrasion properties. Special materials can be added to obtain specific properties such as electrical
conductivity. Polyether PUs are more resistant to hydrolysis than their polyester counterparts, giving them
better water resistance.
In general, Polyurethane is highly abrasion-resistant, from a hardness of 65 Shore A through to 75 Shore D!
They are resistant to oxidation, ozone, sunlight & petroleum-based fuels & oils. PUs are generally considered to
be chemical resistant polymers. Strong acids, alkalis and some strong solvents are to be avoided. Polyurethane
finds continuous use in temperatures of up to 90°C with excursions to as high as 150°C. The resilience of PUs
vary dramatically & can be tailored for specific applications.
TPE INJECTION MOLDING
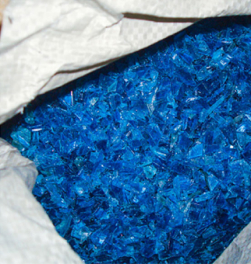
- TPEs are highly flexible and a higher tensile strength.
- Thermoplastic Rubber Material boasts rubber like elasticity and flowable elastomeric properties at high temperatures.
- Since thermoplastic elastomers are pretty soft, they can be stretched to a greater degree without deforming
- The dimensional stability property is another significant property of TPE materials.
WHY WE USE THERMOPLASTIC ELASTOMER MATERIAL FOR INJECTION MOLDING
Several factors should be considered to manufacture the best product. The same goes with injection molding
too. One of the significant reasons to use thermoplastic elastomers is their excellent malleability. This means it
can be easily molded due to its soft texture. Now, let’s dig into a few other benefits you should consider.
The thermoplastic elastomers have the best
colorability properties. And also, it can be over-
molded on various polymers like Polypropylene
and a lot more.
It’s resistant to cleaners and is highly flexible.
So, the production process with TPE is a
cakewalk when compared to liquid silicone
rubber or TPUs.
Another reason to use TPE for injection molding
is its recyclable and degradable properties. The
TPE remains can be used even for multiple
purposes. Meanwhile, it degrades into the soil
after usage making it a more
PROCESSING
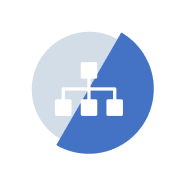
15,000Sq. ft modern, well laid out manufacturing & testing facilities with advanced machinery & Equipments.
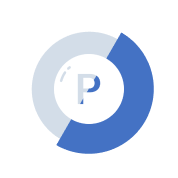
Advanced Auto-dispensing casting machines of capacity 300/500 litres & TPE Injection Molding machines with 5X5 ft Heating chambers & ovens.

Highly trained & skilled production & quality team to manufacture & process 10+ products every day.

Plant capacity of processing 5 metric ton polyurethane & delivering 20+ products on-time every month.